Motor Control Software Development Kit¶
The MotorControl SDK (MC SDK) is a cohesive set of software infrastructure, tools, and documentation designed to minimize C2000 real-time controller based motor control system development time targeted for various three-phase motor control applications. The software includes firmware that runs on C2000 motor control evaluation modules (EVMs) and TI designs (TIDs) which are targeted for industrial drives, robotics, appliances, and automotive applications. MotorControl SDK provides all the needed resources at every stage of development and evaluation for high performance motor control applications.
MC SDK has the latest sensored servo, sensorless InstaSPIN-FOC and sliding mode observer solutions, real-time connectivity examples, incremental and absolute encoders, and the Fast Current Loop (FCL) optimized software library.
The MC SDK is built on top of C2000Ware and is available for download from C2000WARE-MOTORCONTROL-SDK. The SDK is also available online via the TI Resource Explorer for C2000 MC SDK. For a list of supported devices, kits, and reference designs, see the latest MC SDK release notes.
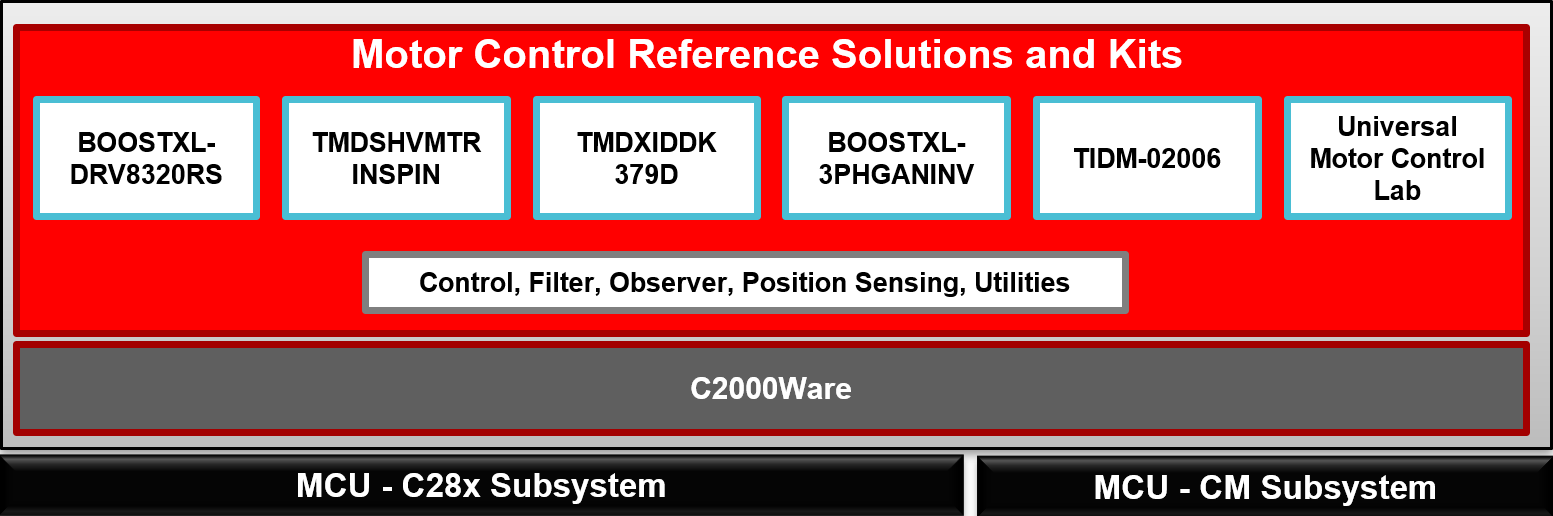
Fig. 6 Motor Control SDK¶
Features¶
Complete software repository for C2000 MCU Motor Control Applications
Sensorless solutions
Sensorless Torque or Velocity
Trapezoidal or Field Oriented Control
Enhanced sliding mode observer for open solution, best for high-speed applications
InstaSPIN-FOC
FAST™ software observer for premium rotor Flux, Angle, Speed, and Torque estimationsMotor Parameter Identification
Motor Parameter Identification
Observer and torque control loop automatic tuning
Premium performance for low-speed and highly dynamic applications
Reference designs may include the following examples
Send commands through CAN interface, potentiometer analog input, and frequency input
System protection
Flying start
Field Weakening
Stall detection and recovery
Start-up failure detection and recovery
Lost phase detection/protection
Motor stop with brake
Vibration and acoustic compensation
Initial Position Detection
Maximum Torque Per Amp (MTPA) for IPM motors
Sensored FOC solutions
Sensored Velocity or Position Field Oriented Control
Position feedback: Resolver, Incremental and Absolute Encoders
Current sense techniques: Low-side shunt, in-line current sampling, and sigma-delta filter demodulation
Fast Current Loop (FCL): Optimized software library that takes full advantage of hardware resources to accelerate the sampling, processing, and actuation of the system to achieve the highest control bandwidth for a given PWM frequency in servo control applications.
Real-time connectivity examples (EtherCAT, CAN, CAN-FD, FSI)
Decentralized / Distributed architecture examples
Use of Configurable Logic Block for absolute encoders, pulse train input/output, QEP decode, and dead-band compensation
Supported Solutions¶
Table 3 summarizes key kits supported in the Motor Control SDK. Please check the latest MC SDK release notes for an up to date list of solutions.
EVM / TI Design |
C2000™ SoC |
Description |
---|---|---|
F2838x, F28004x, F28002x |
Distributed multi-axis servo drive over fast serial interface (FSI) reference design |
|
F2837x, F28004x |
Dual-axis motor drive using fast current loop (FCL) and SFRA on a single MCU reference design |
|
F280013x, F28002x, F28003x |
Dual motor control with digital interleaved PFC for HVAC reference design |
|
F28003x |
High-voltage EV/HEV HVAC eCompressor motor control reference design |
|
F280013x, F28002x, F28003x |
Single project example for different Sensorless (FAST, eSMO, InstaSPIN-BLDC), Sensored (Incremental Encoder, Hall), and control techniques (FOC, Trapezoidal) |
|
F28004x |
InstaSPIN-FOC labs for F28004x FAST ROM |
|
F2838x, F2837x, F28004x, F28002x |
Quick response control of PMSM using Fast Current Loop on the DesignDRIVE Development Kit |
|
Position Encoders |
F2838x, F2837x, F28004x, F28002x, F28003x |
Implemented using Configuration Logic Block and / or other peripherals of C2000 devices T-format Master, PTO – QEP, PTO – PulseGen, PTO – QEP Div, PTO – Abs2QEP |
Servo drive with CAN |
F28002x, F28003x, F28004x |
Sensored FOC motor drive using QEP with integrated CAN communication to control the motor |